How a Process Improvement Plan Can Lead to Long-Term Success
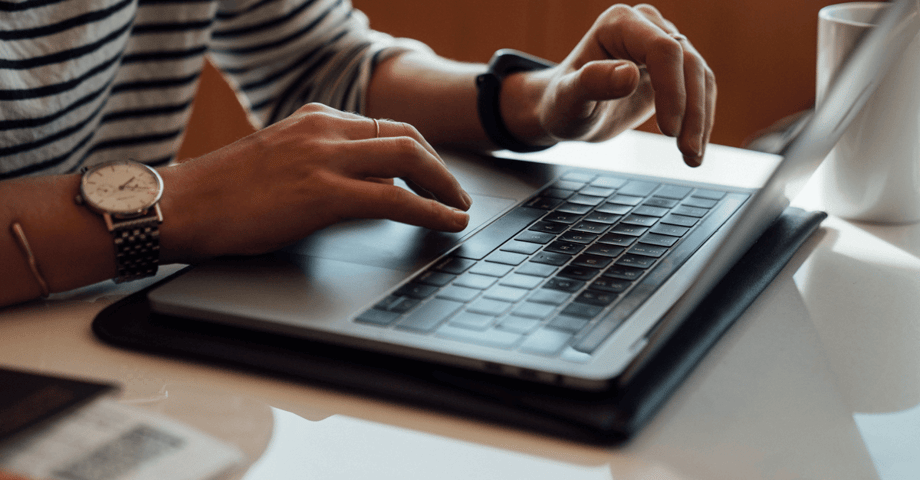
Processes are key to the smooth running of any project. Yet, despite their importance, good processes are incredibly difficult to nail down. What’s more, a business’s processes are often treated as if they cannot be changed. As a project manager, you’ve likely heard the phrase "that’s just how we do things" bandied about in most places of work. But what if we were to tell you that this type of complacency could be holding you and your team back from success?
The short of it is that good processes are critical to long-term success and no process is ever set in stone. The best processes are flexible, and the best teams are willing to evaluate their ways of working on a regular basis with the goal of improving their effectiveness and accuracy. That’s where a process improvement plan comes in handy.
- What is a Process Improvement Plan?
- What are the Benefits of Creating a Process Improvement Plan?
- What are the Steps to Creating a Process Improvement Plan?
- How to Choose a Process Improvement Methodology
- How Forecast Can Help You Implement Your Process Improvement Plan
What is a Process Improvement Plan?
A process improvement plan is a simple document that summarises how your team can improve its processes in relation to project management. In order to create this document, you must first identify what your current processes are and analyze them, considering what works and what doesn't.
This document will help your team be more transparent about processes, understand their functions better and assess opportunities for improvement. It’s important to note that a process improvement plan needn’t be built in one day; completing such a plan is an iterative process that you will work on throughout a project’s run. Plus, the more improvement plans you create, the higher your chances of project success are.
What are the Benefits of Creating a Process Improvement Plan
Higher Efficiency
Issues with efficiency often come down to poor processes. Common issues include members of staff being unclear on approval or sign-off processes, work sitting unassigned because it hasn’t been established who is responsible for assigning new tasks, or outdated processes that include redundant steps preventing projects from moving forward. A process improvement plan can help identify and rectify these issues with actionable steps.
Increased Productivity
A process improvement plan seeks to prevent bottlenecks that halt progress from occurring. It can also help strengthen any weak points in your operations. Not only will reducing bottlenecks help work flow through the business more efficiently, but improved processes can remove friction between different departments or areas of the business, supporting teams to work together in harmony.
All-Round Employee Wellbeing
When processes are clear, employees are saved a great deal of time and stress. Wasting time and money due to poor ways of working can feel frustrating and demoralizing, especially when they result in employees needing to take on tedious and unnecessary tasks. Improved processes can cut down on the amount of time employees spend searching for documents, chasing sign-off, or feeling uncertain about next steps, resulting in streamlined workloads and a happier work environment.
Reduced Risk
Old-school processes, such as manually inputting data into spreadsheets or slow to load software, not only harm the wellbeing of employees but can be detrimental to the quality of work produced by businesses. It is essential to manage risk as mistakes caused by outdated processes can take hours, if not days, to rectify and are more likely to result in project failure due to human error.
More Opportunity for Innovation
Improved processes mean employees will be wasting less time on mundane tasks, affording them more time and headspace to work on what matters. That equals greater opportunities for innovation and planning for the future.
What are the Steps to Creating a Process Improvement Plan?
Now that we understand what a process improvement plan is and how it can benefit a business let’s dive into the steps that it takes to create one. While there are multiple ways to approach or layout your process improvement plan, these key steps should form the basis of your template.
Map
The first step is to identify the processes that you want to improve and map out the current steps that make up each process. We recommend that you do this visually.
Analyze
Now that you have a clear view of all the steps in your processes, it’s time to analyze them. Go through each step with your team and identify where problems most often occur. You may, for example, discover that the planning process usually goes smoothly, but you almost always run into delays when it comes to getting approvals or implementing plans. Other areas to note will be those where you spend a lot of money, hit bottlenecks, or use more resources than should be necessary.
Redesign
Next comes removing the problems you’ve noted from the equation. We always recommend keeping your team informed during this step or working through it with them collaboratively. There’s nothing worse than having to adhere to new processes that you weren’t consulted on!
Keeping your team informed will also ensure you haven’t missed anything important and that you understand their experiences. Work together to brainstorm improvements and possible solutions. Not all solutions will be viable, so you should always analyze these and consider the risks they introduce before moving forward.
Resource
Most, if not all, of your team members and closely linked departments will be affected by changes to your processes. If you are considering making changes at a business level, then everyone will need to be made aware of these.
This step asks you to consider who will be responsible for ensuring the changes are actioned. You will likely need to lean on representatives from every team that will be impacted by the changes in order to keep things running smoothly. Once you’ve identified who these individuals are and what they’ll be responsible for, take the time to explain the new processes to them and how these will benefit the business.
Implementation
Now comes the hard part: implementing your new processes! We recommend starting with a plan that outlines the changes and how you envision them becoming a reality. Include as much detail as possible and get feedback from the individuals you have called upon to help you in the Resource step.
This plan should also include the specific tasks each of your agreed resources will be responsible for and a timeline that lays out when each task will aim to kick-off and when it’ll be completed. This will help with accountability and go a long way to ensuring you hit your deadlines. You can even include key milestones that can be ticked off as you progress.
Communication
This is where your hard work finally pays off, and you get to put your plan into action. Before you begin, it’s key that the plan is shared with your team.
As mentioned, some individuals can be understandably resistant to change, whether because they’re used to old ways of working or because they don’t understand the need for the change. This time is important for smoothing over these bumps by educating your team on the need for improved processes and providing the opportunity to ask questions.
Monitoring & Optimization
This final stage is all about monitoring how well your team adheres to the new process and analyzing the results of your changes.
Process improvement is an iterative process. You will likely need to complete these steps again in the future as the business evolves and your team changes. Don’t be disheartened; continuous improvement will only help you and your team work smarter and produce better results.
How to Choose a Process Improvement Methodology
You may be comfortable using your instinct to guide your process improvement plan. However, if you would prefer to have some guidance in how to implement your plan, one of these methodologies may be for you.
Six Sigma
Six Sigma seeks to reduce the number of variations within your end product. Bill Smith, an engineer and Motorola employee developed this methodology in 1986, using data to measure how well processes work. The priorities here are consistency and customer satisfaction, so it’s no surprise that Six Sigma is popular in the manufacturing industry.
Lean Manufacturing
Lean manufacturing, also known as just-in-time production, was first identified in The Machine That Changed the World by James P. Womack, Daniel Jones, and Daniel Roos. The benefits include reduced wastage that, in turn, results in reduced costs. This methodology follows five principles:
- Identify value
- Value stream mapping
- Create flow
- Establish pull
- Continuous improvement.
Total Quality Management
Total Quality Management (TQM) gained popularity in the 1980s when it was used by the US Federal Government. Here, the focus is on customer satisfaction, with organizations generally following these principles;
- Using systematic and strategic approaches to goals
- Quality is determined by customer satisfaction
- All employees work towards shared goals
- All process steps are defined and performance is monitored for errors or deviations.
Theory of Constraints
The Theory of Constraints (TOC) was popularized by Dr. Eliyahu Goldratt in the 1980s. This methodology focuses on identifying the most significant factor that prevents a goal from being achieved and working systematically to improve the constraint up until the point at which it is no longer stopping the goal from being met. The steps that make up this systematic approach are:
- Identify the constraint
- Decide how to exploit the constraint
- Subordinate and synchronize to the constraint
- Alleviate the constraint
- Repeat as necessary
How Forecast Can Help You Implement Your Process Improvement Plan
Are you ready to begin creating your process improvement plan and helping your business become more efficient, collaborative, and innovative? Here’s how you can use Forecast to improve your processes.
Make Your Plan Visual
With easy-to-use dashboards that allow you to review project progress at a glance, Forecast provides a birds-eye view of your processes, making it easier than ever to identify where your projects regularly experience bottlenecks, overspend, and or are poorly resourced.
Make Your Plan Clear
Regardless of how well-intended a process change is, if its need or function is not clear to your team, it won’t be long before they start reverting to old habits. Keep things clear with simplified resource management, accounting, and project management with Forecast.
Share Your Plan Widely
Forecast is an all-in-one project operation solution that encourages collaboration. When you implement your new processes, be sure to share them widely with your team and keep everyone informed of how the changes are helping the business’s long-term goals.
Sign up for a 14-day trial of Forecast below to maximize your projects’ efficiency with improved processes.
You might like to read these articles on our blog..
Subscribe to the Forecast Newsletter
Get a monthly roundup of productivity tips & hacks delivered straight to your inbox